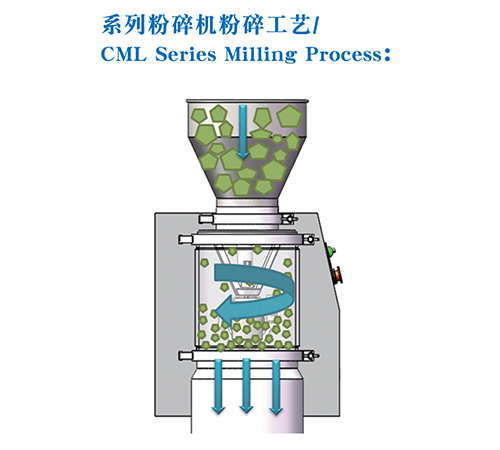
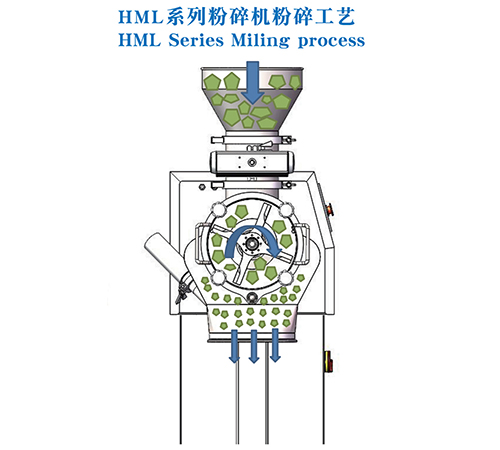
ಕೋನ್ ಮಿಲ್ಲಿಂಗ್
ಕೋನ್ ಗಿರಣಿಗಳು, ಅಥವಾ ಶಂಕುವಿನಾಕಾರದ ಪರದೆಯ ಗಿರಣಿಗಳು, ಏಕರೂಪದ ರೀತಿಯಲ್ಲಿ ಔಷಧೀಯ ಪದಾರ್ಥಗಳ ಗಾತ್ರವನ್ನು ಕಡಿಮೆ ಮಾಡಲು ಸಾಂಪ್ರದಾಯಿಕವಾಗಿ ಬಳಸಲಾಗುತ್ತದೆ. ಆದಾಗ್ಯೂ, ಅವುಗಳನ್ನು ಮಿಶ್ರಣ, ಜರಡಿ ಮತ್ತು ಪ್ರಸರಣಕ್ಕೆ ಸಹ ಬಳಸಬಹುದು. ಅವು ವಿವಿಧ ಗಾತ್ರಗಳಲ್ಲಿ ಬರುತ್ತವೆ, ದೊಡ್ಡ ಔಷಧೀಯ ಸಂಸ್ಕರಣಾ ಕಾರ್ಯಾಚರಣೆಗಳಿಗಾಗಿ ಬಳಸಲಾಗುವ ಪೂರ್ಣ-ಪ್ರಮಾಣದ, ಹೆಚ್ಚಿನ ಸಾಮರ್ಥ್ಯದ ಯಂತ್ರಗಳಿಗೆ ಟೇಬಲ್ಟಾಪ್ ಪ್ರಯೋಗಾಲಯ ಸಾಧನಗಳು ಸೇರಿದಂತೆ.
ಕೋನ್ ಮಿಲ್ಗಳ ಬಳಕೆಗಳು ಬದಲಾಗುತ್ತಿರುವಾಗ, ಔಷಧೀಯ ಉತ್ಪನ್ನಗಳಲ್ಲಿ ಅವುಗಳನ್ನು ಬಳಸುವ ಪ್ರವೃತ್ತಿಯು ಉತ್ಪಾದನೆಯ ಸಮಯದಲ್ಲಿ ಡಿ-ಲಂಪಿಂಗ್ ಒಣಗಿದ ವಸ್ತುಗಳನ್ನು ಒಳಗೊಂಡಿರುತ್ತದೆ; ಒಣಗಿಸುವ ಮೊದಲು ಆರ್ದ್ರ ಕಣಗಳ ಗಾತ್ರ; ಮತ್ತು ಒಣಗಿಸಿದ ನಂತರ ಮತ್ತು ಟ್ಯಾಬ್ಲೆಟ್ ಮಾಡುವ ಮೊದಲು ಒಣ ಹರಳಾಗಿಸಿದ ಕಣಗಳನ್ನು ಅಳತೆ ಮಾಡುವುದು.
ಇತರ ಮಿಲ್ಲಿಂಗ್ ತಂತ್ರಜ್ಞಾನಗಳಿಗೆ ಹೋಲಿಸಿದರೆ, ಕೋನ್ ಗಿರಣಿಯು ಔಷಧೀಯ ತಯಾರಕರಿಗೆ ಇತರ ನಿರ್ದಿಷ್ಟ ಪ್ರಯೋಜನಗಳನ್ನು ನೀಡುತ್ತದೆ. ಈ ಪ್ರಯೋಜನಗಳಲ್ಲಿ ಕಡಿಮೆ ಶಬ್ದ, ಹೆಚ್ಚು ಏಕರೂಪದ ಕಣದ ಗಾತ್ರ, ವಿನ್ಯಾಸ ನಮ್ಯತೆ ಮತ್ತು ಹೆಚ್ಚಿನ ಸಾಮರ್ಥ್ಯ ಸೇರಿವೆ.
ಇಂದು ಮಾರುಕಟ್ಟೆಯಲ್ಲಿನ ಅತ್ಯಂತ ನವೀನ ಮಿಲ್ಲಿಂಗ್ ತಂತ್ರಜ್ಞಾನವು ಹೆಚ್ಚಿನ ಥ್ರೋಪುಟ್ ಮತ್ತು ಉತ್ಪನ್ನದ ಗಾತ್ರದ ವಿತರಣೆಯನ್ನು ನೀಡುತ್ತದೆ. ಹೆಚ್ಚುವರಿಯಾಗಿ, ಅವು ವೇರಿಯಬಲ್ ಜರಡಿ (ಪರದೆ) ಮತ್ತು ಇಂಪೆಲ್ಲರ್ ಆಯ್ಕೆಗಳೊಂದಿಗೆ ಲಭ್ಯವಿದೆ. ಕಡಿಮೆ-ಸಾಂದ್ರತೆಯ ವಸ್ತುಗಳೊಂದಿಗೆ ಬಳಸಿದಾಗ, ನೇರವಾದ ಬಾರ್ಗಳೊಂದಿಗೆ ವಿನ್ಯಾಸಗೊಳಿಸಲಾದ ಗಿರಣಿಗಳಿಗೆ ಹೋಲಿಸಿದರೆ ಜರಡಿ 50 ಪ್ರತಿಶತಕ್ಕಿಂತ ಹೆಚ್ಚು ಥ್ರೋಪುಟ್ ಅನ್ನು ಹೆಚ್ಚಿಸಬಹುದು. ಕೆಲವು ಸಂದರ್ಭಗಳಲ್ಲಿ, ಬಳಕೆದಾರರು ಗಂಟೆಗೆ 3 ಟನ್ಗಳಷ್ಟು ಘಟಕ ಉತ್ಪಾದನಾ ಸಾಮರ್ಥ್ಯವನ್ನು ಸಾಧಿಸಿದ್ದಾರೆ.
ಧೂಳು-ಮುಕ್ತ ಕೋನ್ ಮಿಲ್ಲಿಂಗ್ ಸಾಧಿಸುವುದು
ಮಿಲ್ಲಿಂಗ್ ಧೂಳನ್ನು ಉತ್ಪಾದಿಸುತ್ತದೆ ಎಂದು ತಿಳಿದಿದೆ, ಇದು ಧೂಳನ್ನು ಒಳಗೊಂಡಿರದಿದ್ದರೆ ನಿರ್ವಾಹಕರು ಮತ್ತು ಔಷಧೀಯ ಸಂಸ್ಕರಣಾ ಪರಿಸರಕ್ಕೆ ವಿಶೇಷವಾಗಿ ಅಪಾಯಕಾರಿಯಾಗಿದೆ. ಧೂಳನ್ನು ತಡೆಯಲು ಹಲವಾರು ವಿಧಾನಗಳಿವೆ.
ಬಿನ್-ಟು-ಬಿನ್ ಮಿಲ್ಲಿಂಗ್ ಸಂಪೂರ್ಣ ಇನ್-ಲೈನ್ ಪ್ರಕ್ರಿಯೆಯಾಗಿದ್ದು, ಕೋನ್ ಗಿರಣಿ ಮೂಲಕ ಪದಾರ್ಥಗಳನ್ನು ಆಹಾರಕ್ಕಾಗಿ ಗುರುತ್ವಾಕರ್ಷಣೆಯನ್ನು ಅವಲಂಬಿಸಿದೆ. ತಂತ್ರಜ್ಞರು ಒಂದು ಬಿನ್ ಅನ್ನು ಗಿರಣಿಯ ಕೆಳಗೆ ಇರಿಸುತ್ತಾರೆ ಮತ್ತು ನೇರವಾಗಿ ಗಿರಣಿಯ ಮೇಲೆ ಇರಿಸಲಾದ ಬಿನ್ ವಸ್ತುಗಳನ್ನು ಗಿರಣಿಯಲ್ಲಿ ಬಿಡುಗಡೆ ಮಾಡುತ್ತದೆ. ಗುರುತ್ವಾಕರ್ಷಣೆಯು ಮಿಲ್ಲಿಂಗ್ ನಂತರ ವಸ್ತುವನ್ನು ನೇರವಾಗಿ ಕೆಳಭಾಗದ ಧಾರಕಕ್ಕೆ ಹಾದುಹೋಗಲು ಅನುವು ಮಾಡಿಕೊಡುತ್ತದೆ. ಇದು ಉತ್ಪನ್ನವನ್ನು ಪ್ರಾರಂಭದಿಂದ ಅಂತ್ಯದವರೆಗೆ ಇರಿಸುತ್ತದೆ, ಜೊತೆಗೆ ಮಿಲ್ಲಿಂಗ್ ನಂತರದ ವಸ್ತುಗಳನ್ನು ಸುಲಭವಾಗಿ ವರ್ಗಾಯಿಸುತ್ತದೆ.
ಮತ್ತೊಂದು ವಿಧಾನವೆಂದರೆ ನಿರ್ವಾತ ವರ್ಗಾವಣೆ, ಇದು ಇನ್-ಲೈನ್ ಪ್ರಕ್ರಿಯೆಯಾಗಿದೆ. ಈ ಪ್ರಕ್ರಿಯೆಯು ಧೂಳನ್ನು ಒಳಗೊಂಡಿರುತ್ತದೆ ಮತ್ತು ಗ್ರಾಹಕರು ಹೆಚ್ಚಿನ ದಕ್ಷತೆ ಮತ್ತು ವೆಚ್ಚ ಉಳಿತಾಯವನ್ನು ಸಾಧಿಸಲು ಸಹಾಯ ಮಾಡಲು ಪ್ರಕ್ರಿಯೆಯನ್ನು ಸ್ವಯಂಚಾಲಿತಗೊಳಿಸುತ್ತದೆ. ಇನ್-ಲೈನ್ ವ್ಯಾಕ್ಯೂಮ್ ವರ್ಗಾವಣೆ ವ್ಯವಸ್ಥೆಯನ್ನು ಬಳಸಿಕೊಂಡು, ತಂತ್ರಜ್ಞರು ಕೋನ್ನ ಗಾಳಿಕೊಡೆಯ ಮೂಲಕ ವಸ್ತುಗಳನ್ನು ಪೋಷಿಸಬಹುದು ಮತ್ತು ಅವುಗಳನ್ನು ಸ್ವಯಂಚಾಲಿತವಾಗಿ ಗಿರಣಿಯ ಔಟ್ಲೆಟ್ನಿಂದ ಎಳೆಯಬಹುದು. ಹೀಗಾಗಿ, ಪ್ರಾರಂಭದಿಂದ ಅಂತ್ಯದವರೆಗೆ, ಪ್ರಕ್ರಿಯೆಯು ಸಂಪೂರ್ಣವಾಗಿ ಸುತ್ತುವರಿದಿದೆ.
ಅಂತಿಮವಾಗಿ, ಐಸೊಲೇಟರ್ ಮಿಲ್ಲಿಂಗ್ ಅನ್ನು ಮಿಲ್ಲಿಂಗ್ ಸಮಯದಲ್ಲಿ ಉತ್ತಮವಾದ ಪುಡಿಗಳನ್ನು ಹೊಂದಲು ಶಿಫಾರಸು ಮಾಡಲಾಗುತ್ತದೆ. ಈ ವಿಧಾನದೊಂದಿಗೆ, ಕೋನ್ ಗಿರಣಿಯು ಗೋಡೆಯ ಫಿಕ್ಸಿಂಗ್ ಫ್ಲೇಂಜ್ ಮೂಲಕ ಐಸೊಲೇಟರ್ನೊಂದಿಗೆ ಸಂಯೋಜಿಸುತ್ತದೆ. ಕೋನ್ ಮಿಲ್ನ ಫ್ಲೇಂಜ್ ಮತ್ತು ಕಾನ್ಫಿಗರೇಶನ್ ಐಸೊಲೇಟರ್ನ ಹೊರಗಿರುವ ಸಂಸ್ಕರಣಾ ಪ್ರದೇಶದಿಂದ ಕೋನ್ ಮಿಲ್ ಹೆಡ್ನ ಭೌತಿಕ ವಿಭಜನೆಯನ್ನು ಅನುಮತಿಸುತ್ತದೆ. ಈ ಸಂರಚನೆಯು ಕೈಗವಸು ಪೆಟ್ಟಿಗೆಯ ಮೂಲಕ ಐಸೊಲೇಟರ್ ಒಳಗೆ ಯಾವುದೇ ಶುಚಿಗೊಳಿಸುವಿಕೆಯನ್ನು ಕೈಗೊಳ್ಳಲು ಅನುಮತಿಸುತ್ತದೆ. ಇದು ಧೂಳಿನ ಒಡ್ಡುವಿಕೆಯ ಅಪಾಯವನ್ನು ಕಡಿಮೆ ಮಾಡುತ್ತದೆ ಮತ್ತು ಸಂಸ್ಕರಣೆಯ ಇತರ ಪ್ರದೇಶಗಳಿಗೆ ಧೂಳಿನ ವರ್ಗಾವಣೆಯನ್ನು ತಡೆಯುತ್ತದೆ.
ಹ್ಯಾಮರ್ ಮಿಲ್ಲಿಂಗ್
ಹ್ಯಾಮರ್ ಗಿರಣಿಗಳನ್ನು ಕೆಲವು ಔಷಧೀಯ ಸಂಸ್ಕರಣಾ ತಯಾರಕರು ಟರ್ಬೊ ಗಿರಣಿಗಳು ಎಂದೂ ಕರೆಯುತ್ತಾರೆ, ಸಾಮಾನ್ಯವಾಗಿ ಸಂಶೋಧನೆ ಮತ್ತು ಉತ್ಪನ್ನ ಅಭಿವೃದ್ಧಿಗೆ, ಹಾಗೆಯೇ ನಿರಂತರ ಅಥವಾ ಬ್ಯಾಚ್ ಉತ್ಪಾದನೆಗೆ ಸೂಕ್ತವಾಗಿದೆ. ಡ್ರಗ್ ಡೆವಲಪರ್ಗಳಿಗೆ ಕಷ್ಟಕರವಾದ ಗಿರಣಿ API ಗಳು ಮತ್ತು ಇತರ ಪದಾರ್ಥಗಳ ನಿಖರವಾದ ಕಣ ಕಡಿತದ ಅಗತ್ಯವಿರುವ ಸಂದರ್ಭಗಳಲ್ಲಿ ಅವರನ್ನು ಹೆಚ್ಚಾಗಿ ಬಳಸಿಕೊಳ್ಳಲಾಗುತ್ತದೆ. ಇದರ ಜೊತೆಗೆ, ಮುರಿದ ಮಾತ್ರೆಗಳನ್ನು ಸುಧಾರಿಸಲು ಪುಡಿಯಾಗಿ ಪುಡಿಮಾಡುವ ಮೂಲಕ ಪುನಃ ಪಡೆದುಕೊಳ್ಳಲು ಸುತ್ತಿಗೆ ಗಿರಣಿಗಳನ್ನು ಬಳಸಬಹುದು.
ಉದಾಹರಣೆಗೆ, ತಪಾಸಣೆಯ ನಂತರ, ಕೆಲವು ತಯಾರಿಸಿದ ಟ್ಯಾಬ್ಲೆಟ್ಗಳು ವಿವಿಧ ಕಾರಣಗಳಿಗಾಗಿ ಗ್ರಾಹಕರ ಮಾನದಂಡಗಳಿಗೆ ಅನುಗುಣವಾಗಿರುವುದಿಲ್ಲ: ತಪ್ಪಾದ ಗಡಸುತನ, ಕಳಪೆ ನೋಟ, ಮತ್ತು ಅಧಿಕ ತೂಕ ಅಥವಾ ಕಡಿಮೆ ತೂಕ. ಅಂತಹ ಸಂದರ್ಭಗಳಲ್ಲಿ, ತಯಾರಕರು ವಸ್ತುಗಳ ಮೇಲೆ ನಷ್ಟವನ್ನು ತೆಗೆದುಕೊಳ್ಳುವ ಬದಲು ಮಾತ್ರೆಗಳನ್ನು ಅವುಗಳ ಪುಡಿ ರೂಪಕ್ಕೆ ಹಿಂತಿರುಗಿಸಲು ಆಯ್ಕೆ ಮಾಡಬಹುದು. ಮಾತ್ರೆಗಳನ್ನು ಮರು-ಮಿಲ್ಲಿಂಗ್ ಮಾಡುವುದು ಮತ್ತು ಅವುಗಳನ್ನು ಮತ್ತೆ ಉತ್ಪಾದನೆಗೆ ಪರಿಚಯಿಸುವುದು ಅಂತಿಮವಾಗಿ ತ್ಯಾಜ್ಯವನ್ನು ಕಡಿಮೆ ಮಾಡುತ್ತದೆ ಮತ್ತು ಉತ್ಪಾದಕತೆಯನ್ನು ಹೆಚ್ಚಿಸುತ್ತದೆ. ಟ್ಯಾಬ್ಲೆಟ್ಗಳ ಬ್ಯಾಚ್ ವಿಶೇಷಣಗಳನ್ನು ಪೂರೈಸದ ಎಲ್ಲಾ ಸಂದರ್ಭಗಳಲ್ಲಿ, ತಯಾರಕರು ಸಮಸ್ಯೆಯನ್ನು ನಿವಾರಿಸಲು ಸುತ್ತಿಗೆ ಗಿರಣಿಯನ್ನು ಬಳಸಬಹುದು.
ಸುತ್ತಿಗೆ ಗಿರಣಿಗಳು ಗಂಟೆಗೆ 1,500 ಕಿಲೋಗ್ರಾಂಗಳಷ್ಟು ಉತ್ಪಾದಿಸುವಾಗ 1,000 rpm ನಿಂದ 6,000 rpm ವರೆಗಿನ ವೇಗದಲ್ಲಿ ಕಾರ್ಯನಿರ್ವಹಿಸಲು ಸಮರ್ಥವಾಗಿವೆ. ಇದನ್ನು ಸಾಧಿಸಲು, ಕೆಲವು ಗಿರಣಿಗಳು ಸ್ವಯಂಚಾಲಿತ ತಿರುಗುವ ಕವಾಟವನ್ನು ಹೊಂದಿದ್ದು, ತಂತ್ರಜ್ಞರು ಮಿಲ್ಲಿಂಗ್ ಚೇಂಬರ್ ಅನ್ನು ಅತಿಯಾಗಿ ತುಂಬದೆ ಪದಾರ್ಥಗಳೊಂದಿಗೆ ಸಮವಾಗಿ ತುಂಬಲು ಅನುವು ಮಾಡಿಕೊಡುತ್ತದೆ. ಮಿತಿಮೀರಿದ ತುಂಬುವಿಕೆಯನ್ನು ತಡೆಗಟ್ಟುವುದರ ಜೊತೆಗೆ, ಅಂತಹ ಸ್ವಯಂಚಾಲಿತ ಆಹಾರ ಸಾಧನಗಳು ಪ್ರಕ್ರಿಯೆಯ ಪುನರಾವರ್ತಿತತೆಯನ್ನು ಹೆಚ್ಚಿಸಲು ಮತ್ತು ಶಾಖ ಉತ್ಪಾದನೆಯನ್ನು ಕಡಿಮೆ ಮಾಡಲು ಮಿಲ್ಲಿಂಗ್ ಚೇಂಬರ್ಗೆ ಪುಡಿಯ ಹರಿವನ್ನು ನಿಯಂತ್ರಿಸಬಹುದು.
ಕೆಲವು ಹೆಚ್ಚು ಸುಧಾರಿತ ಸುತ್ತಿಗೆ ಗಿರಣಿಗಳು ಡ್ಯುಯಲ್-ಸೈಡೆಡ್ ಬ್ಲೇಡ್ ಜೋಡಣೆಯನ್ನು ಹೊಂದಿದ್ದು ಅದು ಆರ್ದ್ರ ಅಥವಾ ಒಣ ಪದಾರ್ಥಗಳ ಕಾರ್ಯಸಾಧ್ಯತೆಯನ್ನು ಹೆಚ್ಚಿಸುತ್ತದೆ. ಬ್ಲೇಡ್ನ ಒಂದು ಬದಿಯು ಒಣ ವಸ್ತುಗಳನ್ನು ಒಡೆದು ಹಾಕಲು ಸುತ್ತಿಗೆಯಾಗಿ ಕಾರ್ಯನಿರ್ವಹಿಸುತ್ತದೆ, ಆದರೆ ಚಾಕುವಿನಂತಹ ಭಾಗವು ಆರ್ದ್ರ ಪದಾರ್ಥಗಳ ಮೂಲಕ ಸ್ಲೈಸ್ ಮಾಡಬಹುದು. ಬಳಕೆದಾರರು ಮಿಲ್ಲಿಂಗ್ ಮಾಡುವ ಪದಾರ್ಥಗಳ ಆಧಾರದ ಮೇಲೆ ರೋಟರ್ ಅನ್ನು ಸರಳವಾಗಿ ತಿರುಗಿಸುತ್ತಾರೆ. ಹೆಚ್ಚುವರಿಯಾಗಿ, ಕೆಲವು ಗಿರಣಿ ರೋಟರ್ ಅಸೆಂಬ್ಲಿಗಳನ್ನು ನಿರ್ದಿಷ್ಟ ಉತ್ಪನ್ನದ ವರ್ತನೆಗೆ ಸರಿಹೊಂದಿಸಲು ಹಿಮ್ಮುಖಗೊಳಿಸಬಹುದು ಆದರೆ ಗಿರಣಿಯ ತಿರುಗುವಿಕೆಯು ಬದಲಾಗದೆ ಉಳಿಯುತ್ತದೆ.
ಕೆಲವು ಸುತ್ತಿಗೆ ಗಿರಣಿಗಳಿಗೆ, ಗಿರಣಿಗೆ ಆಯ್ಕೆ ಮಾಡಲಾದ ಪರದೆಯ ಗಾತ್ರವನ್ನು ಆಧರಿಸಿ ಕಣದ ಗಾತ್ರವನ್ನು ನಿರ್ಧರಿಸಲಾಗುತ್ತದೆ. ಆಧುನಿಕ ಸುತ್ತಿಗೆ ಗಿರಣಿಗಳು ವಸ್ತುವಿನ ಗಾತ್ರವನ್ನು 0.2 mm ನಿಂದ 3 mm ವರೆಗೆ ಕಡಿಮೆ ಮಾಡಬಹುದು. ಪ್ರಕ್ರಿಯೆಯು ಪೂರ್ಣಗೊಂಡ ನಂತರ, ಗಿರಣಿಯು ಪರದೆಯ ಮೂಲಕ ಕಣಗಳನ್ನು ತಳ್ಳುತ್ತದೆ, ಇದು ಉತ್ಪನ್ನದ ಗಾತ್ರವನ್ನು ನಿಯಂತ್ರಿಸುತ್ತದೆ. ಅಂತಿಮ ಉತ್ಪನ್ನದ ಗಾತ್ರವನ್ನು ನಿರ್ಧರಿಸಲು ಬ್ಲೇಡ್ ಮತ್ತು ಪರದೆಯು ಸಂಯೋಗದೊಂದಿಗೆ ಕಾರ್ಯನಿರ್ವಹಿಸುತ್ತದೆ.
ಪೋಸ್ಟ್ ಸಮಯ: ಆಗಸ್ಟ್-08-2022